Austenite, also known as gamma phase iron is a metallic non-magnetic allotrope of iron or a solid solution of iron, with an alloying element. In plain-carbon steel, austenite exists above the critical eutectoid temperature of 1,000 K (1,340 °F); other alloys of steel have different eutectoid temperatures. It is named after Sir William Chandler Roberts-Austen (1843–1902).
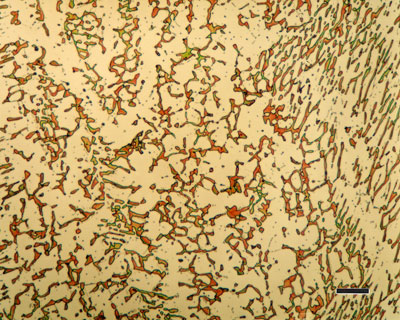
316 austenitic stainless steel, containing sigma phase. Source : https://www.paintertoolinc.com/
Austenite is a metallic, non-magnetic solid solution of carbon and iron that exists in steel above the critical temperature of 1333°F ( 723°C). Its face-centred cubic (FCC) structure allows it to hold a high proportion of carbon in solution. In many magnetic alloys, the Curie point, the temperature at which magnetic materials cease to behave magnetically, occurs at nearly the same temperature as the austenite transformation. This behavior is attributed to the paramagnetic nature of austenite, while both martensite and ferrite are strongly ferromagnetic.
As it cools, this structure either breaks down into a mixture of ferrite and cementite (usually in the structural forms pearlite or bainite), or undergoes a slight lattice distortion known as martensitic transformation. The rate of cooling determines the relative proportions of these materials and therefore the mechanical properties (e.g. hardness, tensile strength) of the steel.
Iron-carbon phase diagram, showing the conditions under which austenite is stable in carbon steel.
Austenite can contain far more carbon than ferrite, between 0.8% at 1333°F (723°C) and 2.08% at 2098°F (1148°C). Thus, above the critical temparture, all of the carbon contained in ferrite and cementite (for a steel of 0.8% C) is dissolved in the austenite. From 912 to 1,394 °C (1,674 to 2,541 °F) alpha iron undergoes a phase transition from body-centred cubic (BCC) to the face-centred cubic (FCC) configuration of gamma iron, also called austenite. This is similarly soft and ductile but can dissolve considerably more carbon (as much as 2.04% by mass at 1,146 °C (2,095 °F)). This gamma form of iron is exhibited by the most commonly used type of stainless steel for making hospital and food-service equipment.
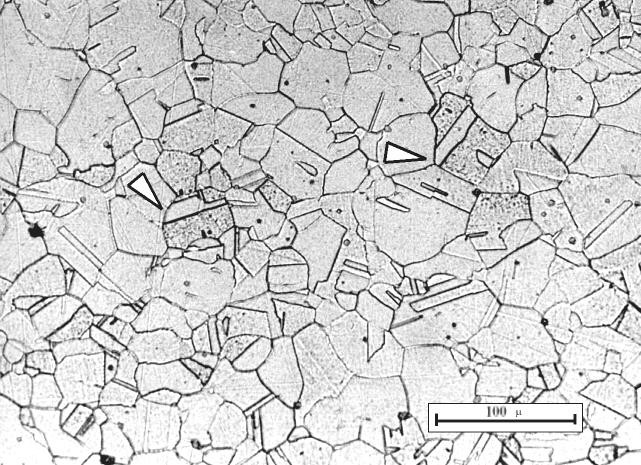
The austenitic structure has good creep resistance and good oxidation resistance
Quenching (to induce martensitic transformation), followed by tempering (to break down some martensite and retained austenite), is the most common heat treatment for high-performance steels. The addition of certain other metals, such as manganese and nickel, can stabilize the austenitic structure, facilitating heat-treatment of low-alloy steels. In the extreme case of austenitic stainless steel, much higher alloy content makes this structure stable even at room temperature.
The ferritic stainless steel on the left has a body centered cubic (bcc) crystal structure. By adding nickel to this stainless steel the structure changes from bcc to face centered cubic (fcc), which is called austenitic, source : https://www.imoa.info
Austenitization means to heat the iron, iron-based metal, or steel to a temperature at which it changes crystal structure from ferrite to austenite. An incomplete initial austenitization can leave undissolved carbides in the matrix. For some irons, iron-based metals, and steels, the presence of carbides may occur or be present during the austenitization step. The term commonly used for this is two-phase austenitization.
Stainless-steel-304-austenite. Source:Wikimedia
On the other hand, such elements as silicon, molybdenum, and chromium tend to de-stabilize austenite, raising the eutectoid temperature (the temperature where two phases, ferrite and cementite, become a single phase, austenite). The addition of certain alloying elements, such as manganese and nickel, can stabilize the austenitic structure, facilitating heat-treatment of low-alloy steels.
Adding 8% nickel to a ferritic chromium stainless steel makes an austenitic chromium-nickel stainless steel, for example Type 304 stainless steel. Source: https://www.imoa.info/
In the extreme case of
austenitic stainless steel, much higher alloy content makes this structure stable even at room temperature. On the other hand, such elements as silicon, molybdenum, and chromium tend to de-stabilize austenite, raising the eutectoid temperature.
Austenite is only stable above 910 °C (1,670 °F) in bulk metal form. However, the use of a face-centered cubic (fcc) or diamond cubic substrate allows the epitaxial growth of fcc transition metals. The epitaxial growth of austenite on the diamond (100) face is feasible because of the close lattice match and the symmetry of the diamond (100) face is fcc. More than a monolayer of gamma-iron can be grown because the critical thickness for the strained multilayer has been determined and is in close agreement with theory.