Ceramics an Introduction
The 20th century has produced the greatest advancement in ceramics and materials technology since humans have been capable of conceptive thought. As the limits of metal-based systems are surpassed, new materials capable of operating under higher temperatures, higher speeds, longer life factors and lower maintenance costs are required to maintain pace with technological advancements.
Metals, by virtue of their unique properties: ductility, tensile strength, abundance, simple chemistry, relatively low cost of production, case of forming, case of joining, etc. have occupied the vanguard position in regard to materials development. This combination enables large shapes to be made; the Space Shuttle is a typical example of the application of advanced materials and an excellent example of the capability of advanced materials.
It is only during the last 30 years or so, with the advances of understanding in ceramic chemistry, crystallography and the more extensive knowledge gained in regard to the production of advanced and engineered ceramics that the potential for these materials has been realised. This advancement changed the way ceramic systems were viewed.
Techniques previously applied to metals were now considered applicable to ceramic systems. Phase transformations, alloying, quenching and tempering techniques were applied to a range of ceramic systems. Significant improvements to the fracture toughness, ductility and impact resistance of ceramics were realised and thus the gap in physical properties between ceramics and metals began to close. More recent developments in non-oxide and tougher ceramics (e.g. nitride ceramics) have closed the gap even further.
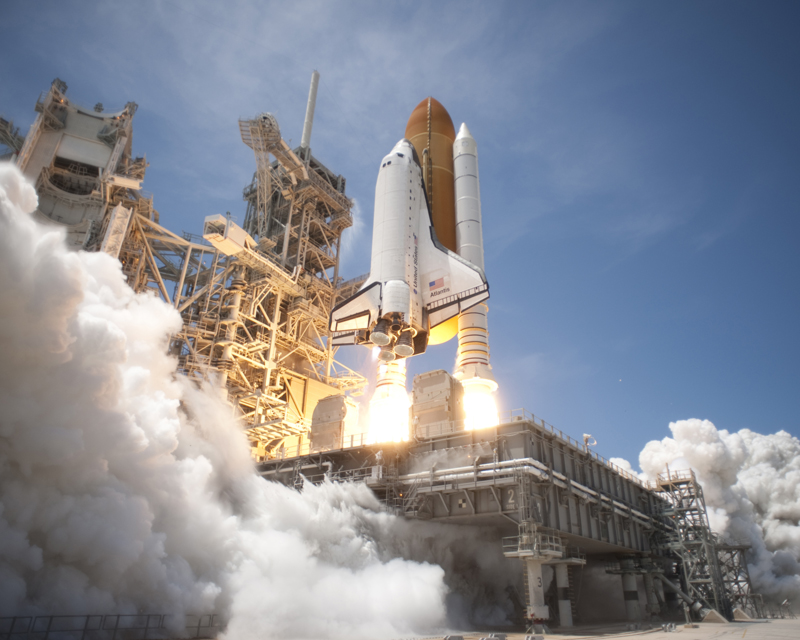
Atlantis will carry aluminium alloy samples for processing in the ISS Materials Science Lab (MSL) furnace. These are metallic rods encapsulated in a ceramic crucible and enclosed in a tantalum metal tube.
Ceramics for today’s engineering applications can be considered to be non-traditional. Traditional ceramics are the older and more generally known types, such as: porcelain, brick, earthenware, etc. The new and emerging family of ceramics are referred to as advanced, new or fine, and utilise highly refined materials and new forming techniques. These “new” or “advanced” ceramics, when used as an engineering material, posses several properties which can be viewed as superior to metal-based systems.
A ceramic is an inorganic, nonmetallic solid prepared by the action of heat and subsequent cooling. Ceramic materials may have a crystalline or partly crystalline structure, or may be amorphous. Technical Ceramics can also be classified into three distinct material categories:
- Oxides: Alumina, zirconia
- Non-oxides: Carbides, borides, nitrides, silicides
- Composites: Particulate reinforced, combinations of oxides and non-oxides.
Each one of these classes can develop unique material properties.
Oxide Ceramics
Oxidation resistant, chemically inert, electrically insulating, generally low thermal conductivity, slightly complex manufacturing and low cost for alumina, more complex manufacturing and higher cost for zirconia.
Non-Oxide Ceramics
Low oxidation resistance, extreme hardness, chemically inert, high thermal conductivity, and electrically conducting, difficult energy dependent manufacturing and high cost.
Ceramic-Based Composites
Toughness, low and high oxidation resistance (type related), variable thermal and electrical conductivity, complex manufacturing processes, high cost.