What is Hydrogen cracking?
Hydrogen cracking also known as cold cracking or delayed cracking. The main feature of this type of crack is that it occurs in ferritic weldable steels, and generally occurs immediately on welding or after a short time after welding, but usually within 48hrs. The mechanism starts with lone hydrogen atoms diffusing through the metal.
At high temperatures, the elevated solubility of hydrogen allows hydrogen to diffuse into the metal (or the hydrogen can diffuse in at a low temperature, assisted by a concentration gradient). When these hydrogen atoms re-combine in minuscule voids of the metal matrix to form hydrogen molecules, they create pressure from inside the cavity they are in. This pressure can increase to levels where the metal has reduced ductility and tensile strength up to the point where it cracks open (hydrogen induced cracking, or HIC). High-strength and low-alloy steels, nickel and titanium alloys are most susceptible. Austempered iron is also susceptible.
Hydrogen cracks can be usually have the following characteristics :
- In C-Mn steels, the crack will normally originate in the heat-affected zone (HAZ) but may also extend into the weld metal.
- Cracks may also occur in the weld bead, normally transverse to the welding direction at an angle of 45 to the weld surface. They are near straight, follow a jagged path.
- In low alloy steels, the cracks can be transverse to the weld, perpendicular to the surface of the weld, but do not branch and are planar (Planar Defect).
On breaking open the weld, the surface of the cracks will normally not be oxidised, even if they are surface breaking, indicating they were formed when the weld was at or near ambient temperature. A slight blue tinge may be seen from the effects of preheating or welding heat.
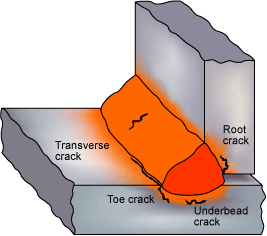
Hydrogen cracks originating in the HAZ and weld metal. (Note that the type of cracks shown would not be expected to form in the same weldment.)
Cracks, which originate in the HAZ, are usually associated with the coarse grain region. The cracks can be intergranular, transgranular or a mixture. Intergranular cracks are more likely to occur in the harder HAZ structures formed in low alloy and high carbon steels. Transgranular cracking is more often found in C-Mn steel structures. In fillet welding, cracks in the HAZ are usually associated with the weld root and parallel to the weld. In butt welds, the HAZ cracks are normally oriented parallel to the weld bead.
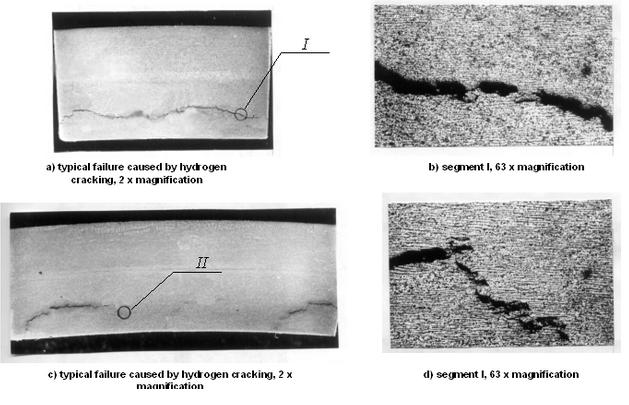
Typical damages caused by hydrogen cracking in pipeline walls detected as a results of ultrasonic testing
There are three factors, which can cause hydrogen cracking:
- Hydrogen generated by the welding process, or by contamination of the weld area.
- A hard brittle structure, which is susceptible to cracking.
- Residual tensile stresses acting on the welded joint (restraint).
- Cracking is caused by the diffusion of hydrogen to the highly stressed, hardened part of the weldment.
In C-Mn steels, because there is a greater risk of forming a brittle microstructure in the HAZ, most of the hydrogen cracks are likely to be found in the parent metal. Using the correct choice of electrodes, the weld metal will have a lower carbon content than the parent metal and, hence, a lower carbon equivalent (CE). However, transverse weld metal cracks can occur especially when welding thick sections.
In low alloy steels, as the weld metal structure is more susceptible than the HAZ, cracking may be found in the weld bead. There are three factors, which can cause hydrogen cracking :
- Hydrogen generated by the welding process, or by contamination of the weld area.
- A hard brittle structure, which is susceptible to cracking.
- Residual tensile stresses acting on the welded joint (restraint).
- Cracking is caused by the diffusion of hydrogen to the highly stressed, hardened part of the weldment.
In C-Mn steels, because there is a greater risk of forming a brittle microstructure in the HAZ, most of the hydrogen cracks are likely to be found in the parent metal. Using the correct choice of electrodes, the weld metal will have a lower carbon content than the parent metal and, hence, a lower carbon equivalent (CE). However, transverse weld metal cracks can occur especially when welding thick sections.